Overview
Zinc cobalt plating provides a high quality, durable finish to steel parts. The zinc coating protects the parts from the effects of wear and tear as well as helping prevent corrosion and abrasion.
The Zinc Cobalt process produces a tough, durable finish with excellent lubricity and far greater resistance to seizure especially useful for moving parts and threaded connections. Lower toxicity of the process and the deposit makes the coating far safer than cadmium.
By electroplating zinc and cobalt to the base metal, the end result is a uniform ductility that will withstand up to six times the corrosion resistance of conventional zinc plating alone.
Suitable Substrate
Steel
Post Treatments
TWB can offer a range of passivates and sealants including;
- Clear / Blue passivate – Trivalent chromate ELV/RoHS compliant
- Yellow Passivate – Hexavalent chromate
- Black Passivate
- Rack Zinc Seal (An organic seal which offers up to + 120 hours to white rust and + 480 Hours to Red rust)
- Electro painted topcoat (Black)
Benefits
- Zinc-Cobalt has far greater corrosion resistance compared to zinc plating alone.
- Even greater corrosion resistance can be achieved by combining the finish with a sealant
- Finished parts have a bright lustre
- Ductility
- Weldability
- Anti-friction
Uses
Zinc-Cobalt’s high resistance to corrosion means it is suitable for use in the most extreme of environments and is also in demand for use on lightweight electric vehicles.
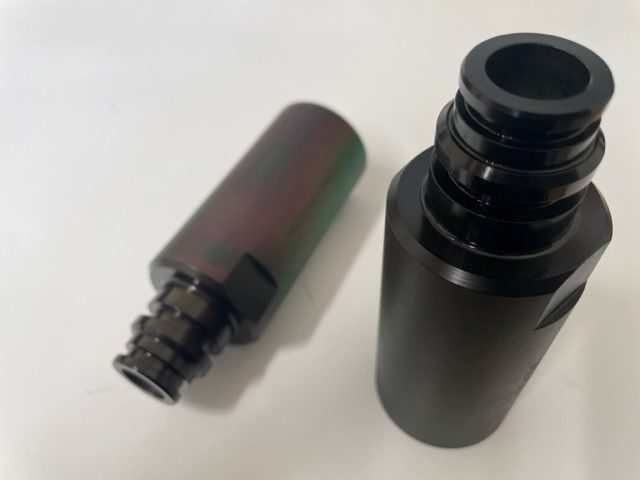
For more information about this service or any other please contact us
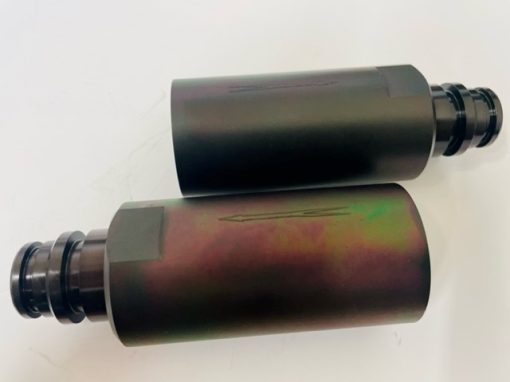
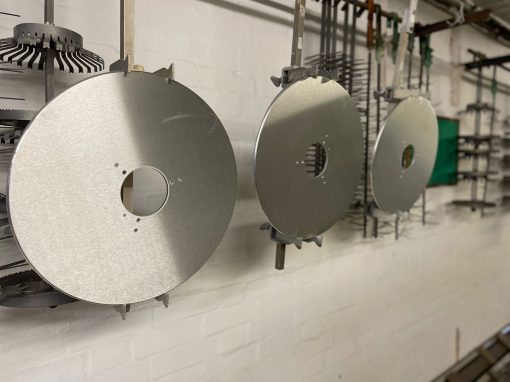
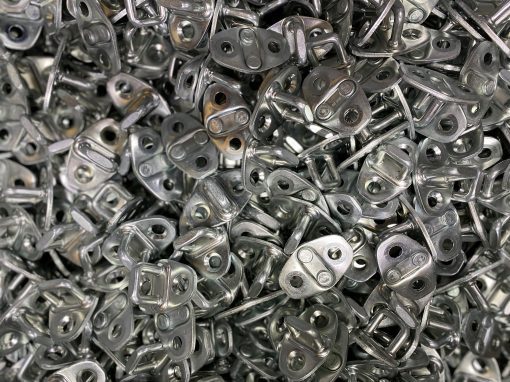
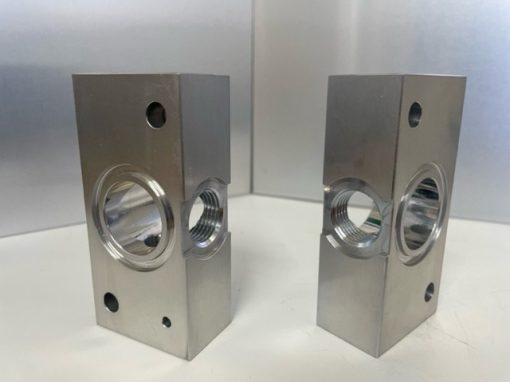
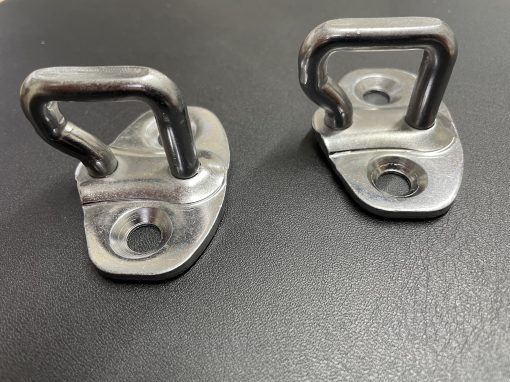
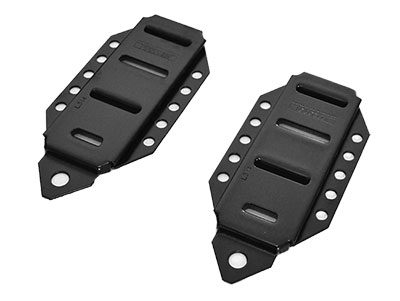