Overview
Anodising is an electrochemical process that converts an aluminium part’s surface into an anodic oxide finish. The anodic oxide finish is composed of a thin layer of aluminium oxide on the surface of the aluminium which slightly increases the thickness of the metal.
The aluminium oxide is fully integrated with the underlying aluminium substrate which means that it wont peel or chip.
Anodising is achieved by immersing the aluminium into an acid electrolyte bath and then passing an electric current through it. A cathode is mounted to the inside of the anodising tank; the aluminium acts as an anode, so that oxygen ions are released from the electrolyte to combine with the aluminium atoms at the surface of the part being anodized. Anodising is effectively a process of highly controlled oxidation.
Work Envelope
600 x 600 x 800
Suitable Substrate
Aluminium
Pre-treatment
Coloured paints and seals can be added to create the desired aesthetic and to further improve durability
Benefits
- It’s easy to maintain; it can be cleaned with water and mild detergents to restore the original lustre,
- UV stable and will not peel or flake, as it is integral to the metal,
- Enhances the durability, wear resistance, hardness, and corrosion resistance of a part.
- Offers an excellent base for secondary processes such as colouring and sealing
- Improves the aesthetic of the finished part by creating a bright shiny surface finish
- Good insulation properties: It improves insulation properties as it produces parts with lower electrical conductivity compared to bare metal.
Uses
- Commercial and residential building products
- Food preparation equipment
- Furniture
- Sporting goods and boats
- Motor vehicle components
- Household appliances
- Consumer electronics and technology
- Electrical engines
- Interior and exterior finishes for construction such as door handles
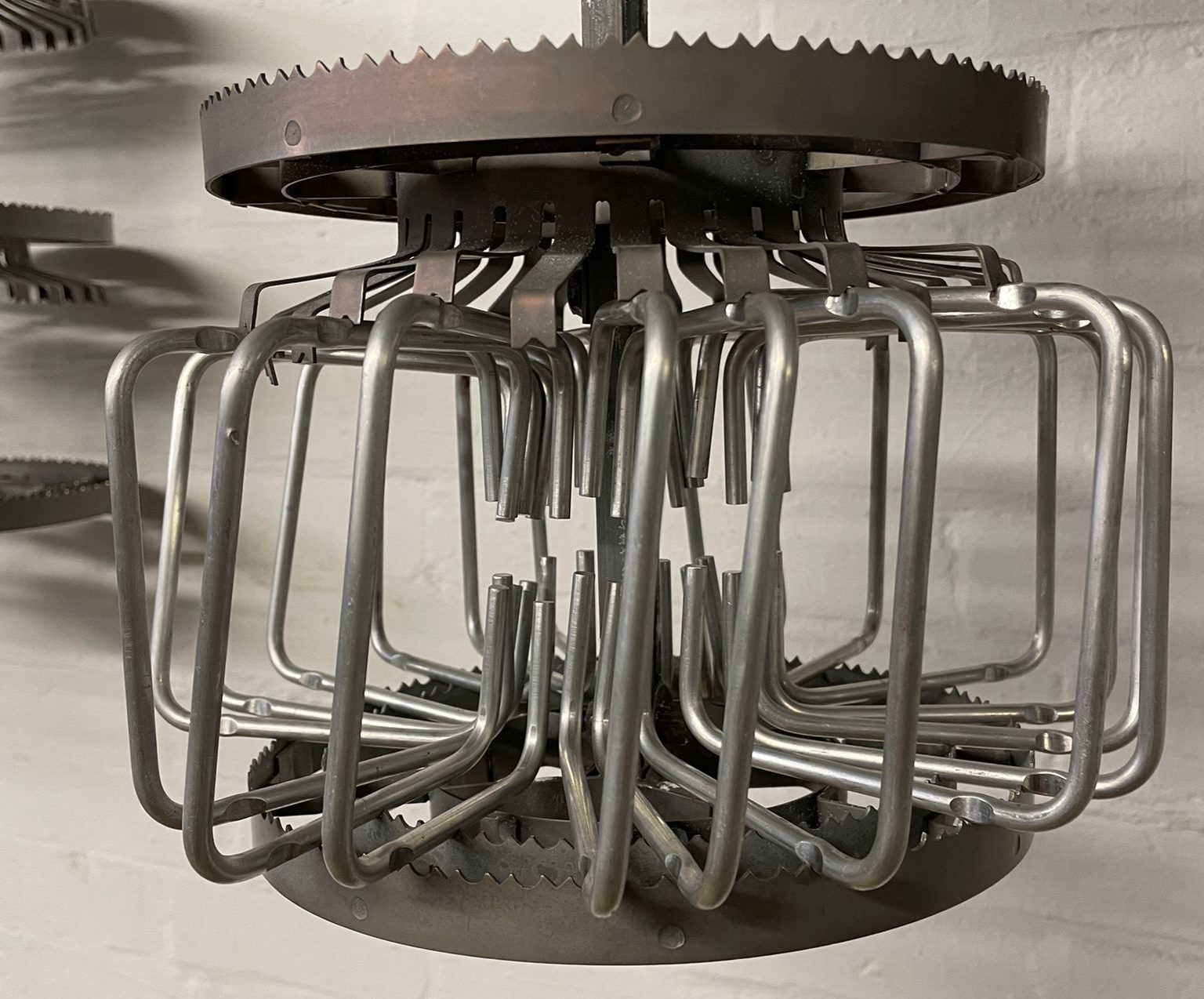
For more information about this service or any other please contact us
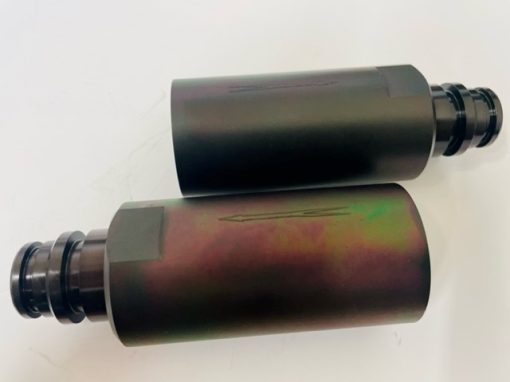
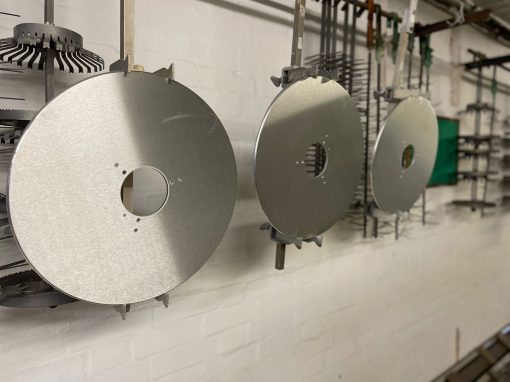
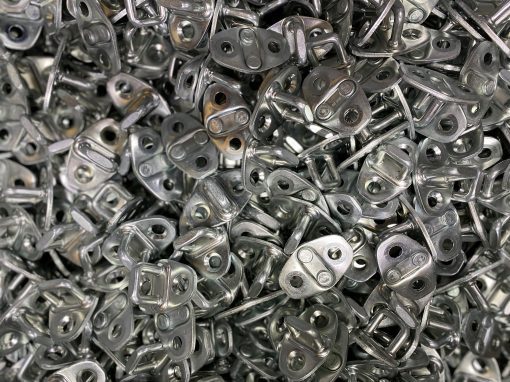
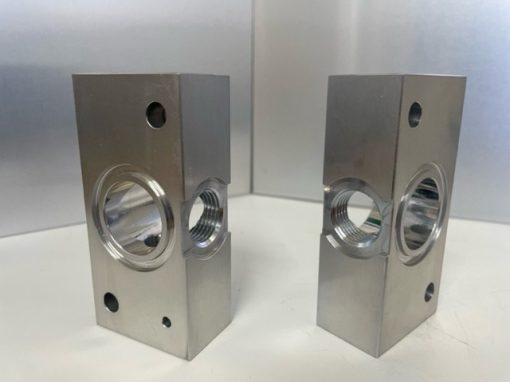
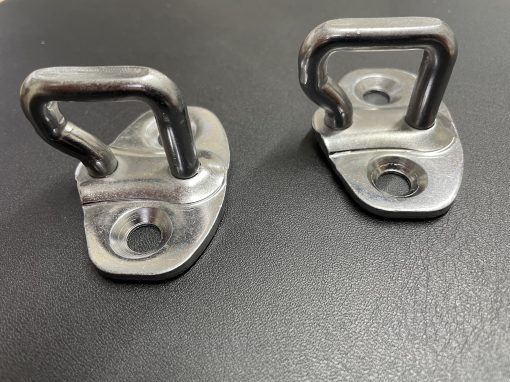
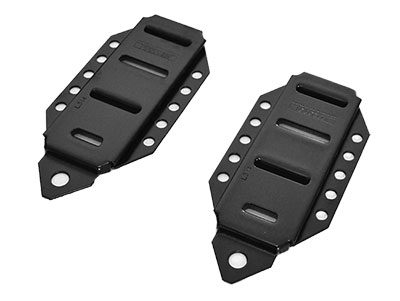